Top 20 Changes in Mining Equipment in 2025

The mining industry is on the brink of transformation in 2025. With rapid advancements in technology, automation, and sustainability, the mining equipment sector is evolving at an unprecedented pace. These changes are not only improving efficiency but also helping address critical challenges such as environmental impact, worker safety, and operational costs. Here are 20 changes in mining equipment to look out for in 2025.
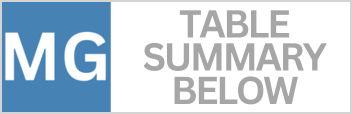
1️⃣ Rise of Autonomous Mining Trucks 🚚
What’s changing:
In 2025, autonomous vehicles will continue to reshape the mining landscape, with self-driving trucks becoming more prevalent in open-pit mining operations. Companies like Caterpillar and Komatsu are investing heavily in autonomous truck fleets that can operate 24/7 without human intervention.
How it works:
- These trucks are equipped with GPS, radar, and cameras to navigate mining roads and transport materials with minimal human oversight.
- They reduce the need for drivers, leading to cost savings in labor and fewer human error-related accidents.
- Autonomous trucks can communicate with other machines to optimize routes and loads, enhancing overall operational efficiency.
The Difference:
Autonomous trucks will dramatically reduce labor costs and improve safety by eliminating humans from hazardous environments. The ability to operate continuously also boosts productivity, making these trucks a game-changer for large mining operations.
2️⃣ Electric-Powered Mining Equipment ⚡
What’s changing:
With increasing pressure to reduce carbon emissions, mining companies are transitioning to electric-powered mining equipment. In 2025, we will see a significant surge in electric-powered excavators, loaders, and haul trucks replacing traditional diesel-powered machines.
How it works:
- Electric mining equipment reduces greenhouse gas emissions and reliance on fossil fuels, making operations more environmentally friendly.
- These machines feature long-lasting lithium-ion batteries that can power large machines through extended shifts.
- Charging stations and infrastructure are being developed to support electric fleets in mines.
The Difference:
By shifting to electric-powered equipment, the mining industry will make significant strides in achieving sustainability goals, reducing their environmental footprint, and potentially lowering operational costs through fuel savings.
3️⃣ AI-Driven Predictive Maintenance 🤖
What’s changing:
Artificial intelligence (AI) is making its way into mining equipment maintenance. In 2025, AI systems will be integrated into machines to predict failures before they happen, ensuring better uptime and reducing unexpected repair costs.
How it works:
- AI algorithms analyze data from sensors embedded in mining equipment to monitor performance and detect anomalies.
- When equipment begins to show signs of wear or potential failure, the system alerts operators and maintenance teams, allowing for timely repairs before a breakdown occurs.
- These systems can optimize the maintenance schedules to avoid downtime and improve equipment lifespan.
The Difference:
Predictive maintenance powered by AI will reduce costly unplanned downtime, improve asset management, and increase the overall efficiency of mining operations by ensuring equipment runs optimally for longer.
4️⃣ Enhanced Safety Features in Mining Equipment 🦺
What’s changing:
Safety continues to be a priority in the mining industry, and 2025 will see new safety features integrated into mining equipment. From collision detection systems to real-time health monitoring of operators, safety will be at the forefront of technological advancements.
How it works:
- New machinery will be equipped with sensors, cameras, and radar to detect and avoid potential hazards, reducing accidents between operators and equipment.
- Advanced monitoring systems will track the health of operators in real-time, alerting supervisors if fatigue or health issues are detected, which can trigger automatic shut-offs or warnings.
- Wearable technology, such as safety helmets and smart vests, will continuously monitor the environment and the operator’s health metrics, such as heart rate and stress levels.
The Difference:
Enhanced safety features not only reduce workplace accidents but also ensure compliance with stricter mining regulations. By keeping workers safe and reducing incidents, mines can improve their operational efficiency and reduce costs related to injuries and lawsuits.
5️⃣ Autonomous Drilling Systems ⛏️
What’s changing:
In 2025, autonomous drilling systems will become increasingly common in both surface and underground mining. These systems will allow drilling machines to operate without direct human intervention, improving speed and accuracy while reducing risks to workers.
How it works:
- Autonomous drilling machines use AI and sensor technology to drill with high precision, adjusting to various soil conditions in real time.
- They can work continuously without breaks, leading to increased productivity.
- The machines are equipped with systems to navigate drilling paths autonomously, avoiding obstacles and adjusting their behavior based on real-time data.
The Difference:
By removing humans from high-risk drilling environments, mining operations can dramatically improve safety. Additionally, autonomous drilling systems will increase the accuracy of drilling operations, reduce waste, and enhance overall mining efficiency.
6️⃣ Smart Mining Sensors and IoT Integration 📡
What’s changing:
As mining operations become more connected, the integration of Internet of Things (IoT) technology in mining equipment is revolutionizing real-time monitoring and data collection. In 2025, the use of sensors embedded in mining machines and equipment will allow for smarter, data-driven decision-making.
How it works:
- Sensors: Advanced sensors placed on mining machinery monitor various factors like temperature, pressure, and vibrations. These sensors collect and transmit data, allowing operators to track the condition of equipment in real-time.
- IoT Integration: The collected data is then fed into a central system via the internet, providing a comprehensive view of the entire operation. Operators can monitor everything from machine performance to environmental conditions like air quality and temperature underground.
The Difference:
This integration allows mines to optimize operations, improve efficiency, and make better, more informed decisions about maintenance and productivity. It also helps detect issues before they become significant problems, reducing downtime and improving safety.
7️⃣ Hybrid Mining Equipment ⚡⛽
What’s changing:
In 2025, hybrid mining equipment, combining both electric and diesel-powered systems, will see wider adoption in the mining industry. These machines will balance energy use, reducing environmental impact while maintaining the power needed for heavy-duty tasks.
How it works:
- Hybrid mining equipment can switch between electric and diesel power depending on the demands of the task, providing the best of both worlds.
- These machines are designed to reduce fuel consumption and emissions while still offering the power needed for intense operations like hauling and excavation.
- The combination of power sources ensures that operations can continue efficiently even in areas where electricity infrastructure is not available.
The Difference:
Hybrid mining machines offer a sustainable alternative to traditional diesel-powered equipment. By reducing reliance on diesel fuel, mines can lower their carbon footprint, reduce operating costs, and increase fuel efficiency. This technology helps meet stricter environmental regulations while maintaining high productivity.
8️⃣ Advanced Excavation Technology 🏗️
What’s changing:
Excavation technology is becoming more advanced with the development of machines that can perform more complex tasks with greater precision. In 2025, we’ll see new excavation machines with greater automation, precision, and efficiency than ever before.
How it works:
- Precision Control: Excavators equipped with advanced sensors, GPS systems, and AI-powered software can dig with much higher precision. This allows for accurate trenching, digging, and earthmoving with minimal human intervention.
- Automation: Advanced excavators can operate autonomously, adjusting their movements and digging depth according to the terrain and task requirements. These machines are often guided by pre-programmed designs and environmental data.
The Difference:
The shift toward automated and highly precise excavation technology leads to faster, more accurate work, minimizing waste and reducing the risk of human error. It also significantly boosts productivity and safety by reducing the need for manual operation in hazardous conditions.
9️⃣ Advanced Dust Control Systems 💨
What’s changing:
Dust is a significant safety and environmental concern in mining, especially in dry, arid environments or underground operations. In 2025, new advanced dust control systems will be implemented in mining operations to significantly reduce airborne dust and improve air quality.
How it works:
- Water-Based Systems: Modern dust control systems use water sprayers and misting devices that automatically apply water to mining areas where dust is most prevalent. This prevents dust from becoming airborne during excavation or hauling.
- Air Filtration Systems: Advanced filtration systems in trucks and equipment cabins will ensure that workers breathe cleaner air. These systems remove fine particles from the air in real time, making it safer for personnel to work in dusty environments.
The Difference:
Dust control is essential for improving worker safety and minimizing environmental impact. Reducing airborne dust lowers the risk of respiratory issues for workers and helps mines comply with stringent environmental standards. It also improves operational efficiency by preventing machinery from becoming clogged with dust.
🔟 Mining Equipment as a Service (MaaS) 🛠️
What’s changing:
The concept of “Mining Equipment as a Service” (MaaS) is gaining traction. Instead of purchasing and maintaining expensive equipment, mining companies will be able to lease mining equipment on demand, significantly reducing capital expenditures.
How it works:
- Leasing Models: Mining companies can subscribe to a fleet of mining equipment based on their needs. They pay for usage rather than ownership, which gives them flexibility and access to the latest technology.
- Data-Driven Maintenance: MaaS providers often offer maintenance as part of the service, using data from sensors and IoT devices to monitor machine performance and ensure everything is running smoothly.
The Difference:
MaaS helps mining companies reduce upfront costs, allowing them to allocate resources more efficiently. By offering the latest and most efficient machines as a service, mining operations can stay competitive without investing heavily in equipment and maintenance.
1️⃣1️⃣ 3D Printing for Mining Equipment Parts 🖨️
What’s changing:
In 2025, the use of 3D printing to manufacture parts for mining equipment will become more widespread. This technology allows for the rapid production of complex, customized parts that were previously costly or time-consuming to produce.
How it works:
- Custom Parts: 3D printing allows manufacturers to create specific parts tailored to the unique needs of mining equipment, such as custom drill bits or replacement components.
- Rapid Prototyping: The technology also allows for faster prototyping, meaning that design flaws can be identified and corrected much quicker, speeding up the development of more efficient mining machines.
- Cost-Efficient: 3D printing significantly reduces the need for large-scale mass production, offering more cost-effective solutions for parts production.
The Difference:
By enabling on-demand production of high-quality, customized parts, 3D printing minimizes downtime and allows for more efficient repairs and replacements. It also reduces the costs associated with traditional manufacturing methods and shipping.
1️⃣2️⃣ Smart Wearable Technology for Miners ⛑️
What’s changing:
Wearable technology will play a pivotal role in improving safety and productivity in mines. By 2025, miners will wear smart devices that monitor vital signs, location, and environmental conditions to improve safety and response times in emergencies.
How it works:
- Health Monitoring: Wearables will track heart rate, fatigue levels, and even temperature, alerting workers to potential health issues such as heatstroke or exhaustion.
- Environmental Sensors: Devices will include sensors that measure gas levels, air quality, and atmospheric pressure, ensuring that miners are safe from hazardous conditions.
- Real-Time Communication: Wearables will allow for constant communication with mining teams and emergency responders, enhancing safety protocols.
The Difference:
Smart wearables offer real-time data that allows mines to proactively respond to hazards, improving worker safety, reducing accidents, and boosting overall operational efficiency.
1️⃣3️⃣ Artificial Intelligence in Mine Site Management 🤖
What’s changing:
AI will be increasingly integrated into mine site management in 2025, helping automate and optimize everything from logistics to resource allocation. AI-driven systems will monitor operations and recommend improvements in real time.
How it works:
- Automated Decision-Making: AI will analyze data from various sources, such as sensor data, equipment performance, and market conditions, to make real-time decisions on how to manage resources more effectively.
- Predictive Analytics: AI systems can predict equipment failures, forecast demand, and even optimize staffing levels, helping improve operational efficiency.
- Automation of Repetitive Tasks: Many routine tasks, such as equipment monitoring and report generation, will be fully automated.
The Difference:
AI allows mining operations to function more efficiently with fewer human errors, optimizing performance, lowering costs, and improving decision-making through data analysis and automation.
1️⃣4️⃣ Drones for Mining Surveys and Inspections 🚁
What’s changing:
Drones will become an integral part of mining operations in 2025, revolutionizing the way mines are surveyed and inspected. They provide real-time aerial data that improves both the accuracy and efficiency of these tasks.
How it works:
- Aerial Surveys: Drones equipped with high-definition cameras and LiDAR sensors will conduct aerial surveys of mining sites, capturing data faster and more safely than traditional ground-based methods.
- Inspection Capabilities: Drones can inspect hard-to-reach areas, such as high walls or unstable ground, providing detailed images and measurements.
- Real-Time Data Transmission: Drones transmit data back to operators in real-time, enabling quick analysis and faster decision-making.
The Difference:
Drones improve surveying and inspection processes by reducing risks to workers, increasing efficiency, and providing more accurate and comprehensive data without the need for costly and time-consuming manual inspections.
1️⃣5️⃣ Advanced Mine Safety Systems ⚠️
What’s changing:
In 2025, the focus on mine safety will continue to evolve with advanced safety systems that integrate sensors, AI, and real-time monitoring to prevent accidents and enhance emergency response.
How it works:
- Environmental Sensors: New systems will be able to detect gases, temperature changes, and vibrations, alerting miners and supervisors to potentially hazardous conditions.
- Automated Shutdowns: In case of dangerous environmental conditions or equipment malfunctions, the system can automatically shut down machinery to prevent accidents.
- Real-Time Alerts: These systems will send real-time alerts to workers and safety teams, enabling faster responses and increasing overall safety.
The Difference:
Advanced safety systems reduce the risk of accidents by providing timely warnings and automatic responses to dangerous conditions, enhancing worker safety and improving the overall operational environment in mines.
1️⃣6️⃣ Hybrid Diesel-Electric Mining Equipment ⚡⛽
What’s changing:
Hybrid diesel-electric technology will continue to transform the mining equipment sector in 2025. This combination of power sources allows equipment to run more efficiently, reducing fuel consumption and emissions.
How it works:
- Dual Power Sources: Hybrid mining machines switch between diesel and electric power depending on the task and conditions. When high power is needed, diesel engines take over; for lighter tasks, electric power is used to save fuel.
- Regenerative Systems: Some hybrid systems feature regenerative braking, where energy is captured during braking and stored for later use, reducing the need for additional fuel.
The Difference:
Hybrid equipment reduces fuel costs and emissions, making operations more sustainable and cost-effective, while maintaining the power and efficiency required for heavy mining tasks.
1️⃣7️⃣ Blockchain for Mining Supply Chain Transparency ⛓️
What’s changing:
Blockchain technology will play a significant role in 2025 by providing greater transparency and security in the mining supply chain. This ensures the authenticity of materials, improves traceability, and reduces fraud.
How it works:
- Decentralized Ledger: Blockchain uses a decentralized, digital ledger to track transactions and shipments in the mining supply chain, making the entire process more transparent.
- Smart Contracts: These blockchain-based contracts automatically execute agreed-upon terms, ensuring that payments and deliveries are handled efficiently and securely.
The Difference:
Blockchain enhances the security and transparency of mining transactions, reducing the risk of fraud and ensuring more ethical sourcing and supply chain practices. It also helps in tracking the origin of minerals and materials for compliance with global standards.
1️⃣8️⃣ Automated Material Handling Systems 🚜
What’s changing:
Automated material handling systems are being increasingly adopted in mining operations in 2025. These systems reduce the need for manual labor while improving the speed and accuracy of material transport.
How it works:
- Robotic Systems: Automated trucks, conveyors, and robotic systems are used to transport mined materials more efficiently, reducing human error and speeding up the entire process.
- AI Optimization: AI is integrated to optimize the flow of materials in real-time, making adjustments based on supply and demand within the mining site.
The Difference:
By automating material handling, mining operations reduce labor costs, increase throughput, and improve safety by minimizing human involvement in high-risk environments.
1️⃣9️⃣ Virtual Reality (VR) for Operator Training 🎮
What’s changing:
Virtual reality will revolutionize how mining companies train operators in 2025. VR simulations will allow workers to practice operating heavy machinery in a safe, controlled environment without the risk of real-world accidents.
How it works:
- Immersive Training: VR creates a fully immersive environment where operators can learn how to use mining equipment, handle emergency scenarios, and understand site-specific procedures without being on-site.
- Real-Time Feedback: Trainees receive real-time feedback on their performance, helping them improve their skills before operating actual machinery.
The Difference:
VR-based training improves operator competence and safety, reducing mistakes in real-world operations and enhancing the overall efficiency of training programs, especially for high-risk activities.
2️⃣0️⃣ Advanced Dust Suppression Technology 💨
What’s changing:
Dust control will be a key focus in 2025 with the introduction of advanced dust suppression technologies that minimize airborne dust and improve air quality in mining environments.
How it works:
- Misting Systems: High-efficiency misting systems will spray fine droplets of water over dusty areas, binding dust particles and preventing them from becoming airborne.
- Dust-Collecting Technology: New equipment will include built-in systems that automatically capture and filter dust particles at the source.
The Difference:
Improved dust suppression technology will significantly enhance worker health and safety by reducing respiratory risks, as well as help mining operations comply with stricter environmental regulations.
The mining industry is undergoing an exciting transformation in 2025, driven by innovation in technology, sustainability, and automation. From autonomous trucks to advanced VR training and hybrid equipment, these changes are improving efficiency, safety, and environmental sustainability across the sector. As these technologies continue to evolve, mining operations will not only be more cost-effective but will also help pave the way for a greener, more responsible industry. Staying ahead of these trends will be crucial for companies looking to remain competitive and meet the growing demand for sustainable practices in mining.
Table Summary
MinerGuide: Top Changes in Mining Equipment for 2025 | |
---|---|
Change | Details |
1️⃣ Autonomous Mining Trucks | Self-driving trucks will dominate in open-pit mining, cutting costs, boosting efficiency, and improving safety. These vehicles operate 24/7, with advanced sensors and AI to reduce human error and optimize delivery routes. |
2️⃣ Electric-Powered Mining Equipment | Electric mining machinery will replace diesel-powered options, reducing emissions, lowering fuel costs, and increasing sustainability in operations. With advancements in battery technology, these machines are set to become more common in 2025. |
3️⃣ AI-Driven Predictive Maintenance | AI systems will predict equipment failures before they happen by analyzing data from sensors in real-time. This tech prevents unplanned downtime, saving costs and improving the efficiency of equipment management. |
4️⃣ Enhanced Safety Features | New safety systems in mining equipment will include collision detection, real-time health monitoring for workers, and automated shutdowns in case of dangerous conditions, dramatically improving on-site safety. |
5️⃣ Autonomous Drilling Systems | In 2025, autonomous drilling rigs will increase precision and reduce human risk. These systems will work around the clock and adjust based on soil conditions, improving drilling accuracy and minimizing errors. |
6️⃣ Smart Mining Sensors and IoT Integration | IoT sensors will allow for real-time tracking and data collection on equipment and environmental conditions, helping operators make smarter decisions, optimize operations, and reduce risks by detecting issues early. |
7️⃣ Hybrid Mining Equipment | Hybrid diesel-electric machines will provide flexibility, allowing mines to save fuel and reduce emissions. These systems automatically switch between diesel and electric depending on the task, optimizing performance. |
8️⃣ Advanced Excavation Technology | Excavators equipped with advanced sensors and AI will improve accuracy in digging, reduce waste, and automate repetitive tasks. These machines are designed for higher productivity and precision in mining operations. |
9️⃣ Advanced Dust Control Systems | New dust control systems will use misting, filtration, and other technologies to drastically reduce airborne dust. These systems will improve air quality on-site, helping workers stay healthier and safer in dusty environments. |
🔟 Mining Equipment as a Service (MaaS) | Mining companies will move towards leasing equipment instead of purchasing it outright. This shift to “Mining Equipment as a Service” will reduce capital expenditure and allow for on-demand access to cutting-edge machinery. |
1️⃣1️⃣ 3D Printing for Mining Equipment Parts | 3D printing will be used for manufacturing custom parts for mining equipment, reducing costs and production time. It allows for on-demand production, especially for hard-to-find or specialized components, improving efficiency in repairs. |
1️⃣2️⃣ Smart Wearable Technology for Miners | Wearables will monitor vital signs, location, and environmental conditions for miners. These devices will track fatigue, heart rate, and temperature, alerting workers and supervisors to potential safety hazards in real-time. |
1️⃣3️⃣ Artificial Intelligence in Mine Site Management | AI will be integrated to monitor and optimize mining operations. It will automate decision-making, forecast demand, schedule maintenance, and analyze performance, allowing managers to make smarter, data-driven decisions quickly. |
1️⃣4️⃣ Drones for Mining Surveys and Inspections | Drones will be used to perform aerial surveys and inspections of mining sites, providing faster and safer data collection. They will map terrains, monitor progress, and identify areas of concern that require attention. |
1️⃣5️⃣ Advanced Mine Safety Systems | New safety systems in mining equipment will include real-time hazard detection and automatic shutdowns for hazardous conditions. This will ensure that workers are protected from risks like gas leaks, equipment malfunctions, and other emergencies. |
1️⃣6️⃣ Hybrid Diesel-Electric Mining Equipment | Hybrid mining equipment, combining electric and diesel power, will reduce emissions and fuel costs. These machines will adjust between fuel sources depending on operational needs, improving efficiency and minimizing environmental impact. |
1️⃣7️⃣ Blockchain for Mining Supply Chain Transparency | Blockchain will be used to track mining materials from source to destination, ensuring transparency and preventing fraud. It will improve traceability, enhance regulatory compliance, and promote ethical sourcing practices in the industry. |
1️⃣8️⃣ Automated Material Handling Systems | Automated conveyor belts, robotic systems, and other material handling solutions will be used to move materials efficiently, reducing human labor and increasing speed in mining operations. Automation will also reduce the risk of workplace injuries. |
1️⃣9️⃣ Virtual Reality (VR) for Operator Training | VR simulations will be used to train mining operators in a safe, controlled environment. This will allow workers to practice using equipment, handle emergencies, and learn safety protocols without putting themselves or others at risk. |
2️⃣0️⃣ Advanced Dust Suppression Technology | New dust suppression systems will use misting and filtration technology to reduce airborne dust in mining environments. This will improve air quality, protect workers’ respiratory health, and ensure compliance with environmental regulations. |