10 Reasons Why High-Purity Quartz is the Backbone of Semiconductors
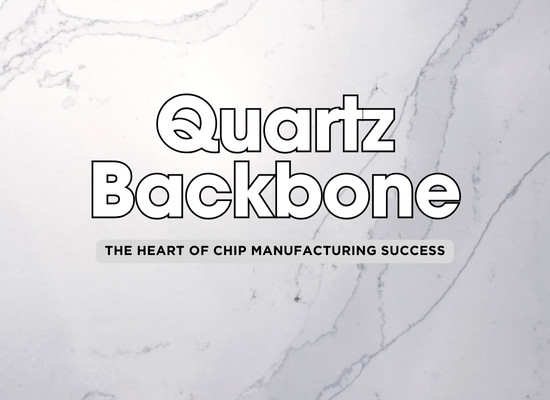
When you think of semiconductors, you probably picture sleek microchips or advanced computer processors. But behind every semiconductor is an unsung hero: high-purity quartz. This unique mineral is a critical raw material for producing the silicon wafers that power everything from smartphones to electric vehicles to AI-powered servers. Its unmatched purity, thermal stability, and optical clarity make it indispensable to the semiconductor supply chain. As the demand for semiconductors grows, so does the race to secure reliable sources of high-purity quartz. Below, we explore 10 key reasons why this vital resource is the backbone of semiconductor manufacturing.
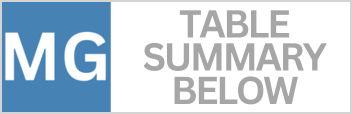
1️⃣ It’s the Primary Source for Silicon Wafers
🔍 Why It Matters: Without high-purity quartz, there are no silicon wafers — and without silicon wafers, there are no semiconductors.
The Details:
High-purity quartz is transformed into ultra-high-purity silicon through a refining process. This silicon is then shaped into wafers that serve as the base for microchips. The purity of the quartz used in this process is crucial, as even microscopic contaminants can affect the performance of the final chip. Semiconductors require a purity level of 99.999% (5N) or higher, and only a handful of quartz sources globally meet this standard. This makes high-purity quartz one of the most sought-after raw materials in the tech industry.
Example in Action:
Silicon wafers used in TSMC’s advanced 5nm chips — found in modern smartphones and AI chips — rely on quartz with ultra-high purity. Without this purity, the chips would suffer from electrical defects, leading to costly production failures.
💡 Insider Insight: Demand for silicon wafers is expected to rise by 14% annually due to the growth of AI, EVs, and IoT devices, driving up the demand for high-purity quartz.
2️⃣ It Provides Thermal Stability in Semiconductor Production
🔍 Why It Matters: Semiconductors are manufactured under extreme heat conditions, and quartz can withstand these temperatures without deformation.
The Details:
During the Chemical Vapor Deposition (CVD) process, semiconductor wafers are exposed to temperatures as high as 1,100°C (2,012°F). To endure this heat, quartz components like crucibles, reactor tubes, and handling rods are used. High-purity quartz has a low thermal expansion coefficient, meaning it doesn’t crack or distort under extreme heat. This thermal stability ensures that every wafer stays perfectly aligned, reducing defects and production errors.
Example in Action:
Without high-purity quartz crucibles, solar-grade silicon — used in solar panels — wouldn’t be possible. The crucibles allow for controlled, stable production, ensuring the silicon stays pure and free of defects. This same principle applies to semiconductor production, where flawless wafer fabrication is essential for next-gen chips.
💡 Insider Insight: Quartz glass crucibles are a multi-million-dollar industry, with global semiconductor fabs like Samsung and Intel relying on them for wafer production. Investing in suppliers of quartz crucibles is a strategic move for investors in the semiconductor supply chain.
3️⃣ It Supports Optical Clarity in Photolithography
🔍 Why It Matters: Photolithography — a key step in semiconductor production — depends on the optical clarity of high-purity quartz lenses.
The Details:
Photolithography involves using ultraviolet (UV) light to etch intricate circuit patterns onto silicon wafers. To direct this light with precision, manufacturers use lenses made from high-purity quartz. Unlike traditional glass, high-purity quartz allows UV light to pass through without distortion or loss of intensity. This clarity ensures that the patterns etched onto the wafer are razor-sharp, even as semiconductors shrink to sizes as small as 2nm or 3nm.
Example in Action:
Next-generation photolithography machines, like those made by ASML, use extreme ultraviolet (EUV) light to print patterns on silicon wafers. The quartz lenses in these machines are so precise that even the smallest imperfection could ruin a multi-million-dollar production batch.
💡 Insider Insight: The market for EUV photolithography equipment is valued at over $14 billion annually, and suppliers of ultra-pure quartz lenses are critical to this industry. The precision required for these lenses will only grow as semiconductor nodes shrink to 1nm and below.
4️⃣ Essential for Plasma Etching and Cleaning
🔍 Why It Matters: Plasma etching, one of the most critical steps in semiconductor production, relies on quartz chambers that can endure high-energy plasma.
The Details:
Plasma etching is a process where plasma (an ionized gas) is used to carve intricate patterns on silicon wafers. This process requires an ultra-clean environment to avoid contamination and a material that can handle repeated exposure to ionized particles. High-purity quartz is the material of choice for etching chambers due to its resistance to plasma erosion and its ability to maintain a contaminant-free environment. Quartz etching chambers can be used for thousands of etching cycles without degradation, ensuring minimal downtime for semiconductor fabs.
Example in Action:
Lam Research and other semiconductor equipment manufacturers rely on quartz chambers in their plasma etching tools. If impurities from lower-grade materials contaminate these chambers, it can lead to wafer defects, costing manufacturers millions of dollars.
💡 Insider Insight: The demand for semiconductor etching tools is skyrocketing as chip manufacturers adopt smaller nodes like 2nm and 1nm. Companies that supply quartz etching chambers are critical to ensuring uninterrupted production of these ultra-small, next-gen chips.
5️⃣ Supports Ultra-High-Purity Production Environments
🔍 Why It Matters: Contamination is the biggest enemy of semiconductor manufacturing, and high-purity quartz is critical for creating ultra-clean production environments.
The Details:
In semiconductor fabs (fabrication plants), cleanliness is paramount. A single speck of dust can destroy an entire wafer, causing production downtime and financial losses. High-purity quartz is used to create essential cleanroom components like quartz tubing, rods, and vessels that transport materials without shedding particles or releasing contaminants. Quartz’s chemical inertness means it won’t react with chemicals, gases, or plasma used in chip production, helping maintain “ultra-clean” manufacturing conditions.
Example in Action:
Companies like Intel and TSMC invest heavily in maintaining ultra-clean production environments. From quartz-handling rods used to transfer wafers to quartz reactor tubes that control chemical reactions, high-purity quartz plays an essential role in ensuring particle-free manufacturing processes.
💡 Insider Insight: Quartz-based cleanroom components are part of the global market for cleanroom consumables, which is projected to exceed $16 billion by 2025. Investing in companies that supply quartz tubing, vessels, and rods could be a strategic entry point into this growing market.
6️⃣ Prevents Contamination During Chemical Vapor Deposition (CVD)
🔍 Why It Matters: Chemical Vapor Deposition (CVD) is a crucial process for applying ultra-thin layers on wafers, and only high-purity quartz can ensure a contaminant-free reaction.
The Details:
CVD is a process where a wafer is coated with ultra-thin layers of material (like silicon, nitrides, or oxides) to create the electrical pathways needed for semiconductors. These coatings must be applied in a 100% pure and controlled environment, free from contamination. High-purity quartz reactor tubes and chambers provide a clean, chemically inert space where the chemical reaction can take place. The quartz material withstands extreme temperatures and corrosive gases without releasing impurities, ensuring perfectly uniform coatings.
Example in Action:
During CVD, wafers are placed in a quartz reactor tube while gases react to form a thin film on the wafer surface. If a reactor is made from lower-grade materials, contaminants from the material itself can bond to the wafer, causing defects. To avoid this, semiconductor fabs rely on ultra-pure quartz reactors from companies like Momentive and Heraeus.
💡 Insider Insight: The market for CVD tools and reactors is expected to grow at a 10% CAGR through 2030, driven by the rise of advanced chip production. Companies producing quartz reactor tubes are uniquely positioned to benefit from this growth.
7️⃣ Critical for Ion Implantation in Wafers
🔍 Why It Matters: Ion implantation is a crucial step in semiconductor production, and quartz components help maintain the purity and precision required for implant accuracy.
The Details:
Ion implantation involves bombarding silicon wafers with ions (charged particles) to alter the electrical properties of the semiconductor. To ensure the ions are implanted at precise depths, the process requires ultra-clean, non-reactive materials to house the wafers. High-purity quartz is used for wafer carriers, ion beam guides, and process chambers. Unlike metals or lower-grade materials, quartz doesn’t release particles or react with the ions, ensuring absolute purity in the implantation process.
Example in Action:
Applied Materials, a leading supplier of semiconductor manufacturing equipment, uses quartz-based wafer carriers and ion implantation chambers in their ion implanters. Without high-purity quartz, the ion implantation process would be plagued by defects, leading to millions of dollars in wasted production.
💡 Insider Insight: Ion implantation is essential for producing transistors in chips used for AI, 5G, and autonomous vehicles. As these industries grow, demand for ultra-pure quartz ion implantation chambers will grow as well.
8️⃣ Essential for Quartz Crucibles Used in Silicon Production
🔍 Why It Matters: Quartz crucibles are the starting point for growing silicon crystals, which are sliced into wafers used in every semiconductor.
The Details:
To create high-purity silicon, manufacturers use quartz crucibles to melt raw quartz at extreme temperatures. This molten silicon is then slowly cooled to form single-crystal silicon ingots, which are later sliced into wafers. The purity of the crucible directly affects the purity of the silicon ingot. If the crucible introduces even a trace amount of contamination, it compromises the entire production batch. High-purity quartz is required to produce flawless crucibles that can endure the high temperatures and maintain chemical stability during the growth process.
Example in Action:
The world’s largest semiconductor producers, including Intel and Samsung, depend on high-purity quartz crucibles to grow monocrystalline silicon for their advanced chips. Major suppliers of quartz crucibles, like Heraeus and Momentive, are vital to this process, and disruptions in supply can delay chip production worldwide.
💡 Insider Insight: The price of monocrystalline silicon is rising due to high demand for both semiconductors and solar panels. Companies supplying quartz crucibles are poised to benefit as production ramps up to meet chip shortages.
9️⃣ Helps Reduce Supply Chain Risks in Semiconductor Manufacturing
🔍 Why It Matters: With chip shortages and geopolitical tensions affecting supply chains, securing access to high-purity quartz is now a top priority for semiconductor fabs.
The Details:
Only a handful of suppliers in the world can produce quartz at the 5N (99.999%) purity required for semiconductor manufacturing. Countries like Norway, Brazil, and the U.S. control the production of this crucial raw material. If these sources face disruptions (due to geopolitics, natural disasters, or supply chain issues), semiconductor production grinds to a halt. To avoid this, semiconductor companies are seeking to vertically integrate their supply chains, investing directly in quartz mining, refining, and purification. This ensures they have access to a steady supply of this mission-critical material.
Example in Action:
When TSMC faced chip production delays, it wasn’t just a lack of silicon — it was also a shortage of the quartz crucibles and tubes used in the production process. By investing in their own supply chains and sourcing quartz from multiple suppliers, companies like Intel and Samsung aim to protect themselves from future supply shocks.
💡 Insider Insight: The push for “supply chain independence” has led to a rise in onshore quartz mining projects in places like North Carolina (U.S.) and Norway. Investors can profit by backing mining projects or investing in companies with exclusive quartz supply contracts.
🔟 Provides the Foundation for Semiconductor Innovation
🔍 Why It Matters: Without high-purity quartz, next-generation semiconductors like 1nm, 2nm, and 3nm chips wouldn’t be possible.
The Details:
The semiconductor industry is advancing rapidly, with 1nm chips expected to be the next big leap in computing power. To achieve this, every step in the manufacturing process — from photolithography to ion implantation — must be precise beyond human capability. High-purity quartz enables these precision processes by supporting extreme temperatures, optical clarity, and ultra-clean environments. As semiconductor nodes get smaller, the tolerance for defects shrinks to nearly zero, making ultra-pure quartz essential for the success of next-gen semiconductor manufacturing.
Example in Action:
The race to produce sub-2nm semiconductors is being led by companies like ASML, TSMC, and Samsung, which rely on extreme ultraviolet (EUV) photolithography. Without quartz lenses and photomasks, EUV lithography would not be possible, meaning the world’s most powerful chips could not be produced.
💡 Insider Insight: As semiconductor nodes shrink to 1nm and beyond, the demand for ultra-high-purity quartz will rise exponentially. Companies that supply EUV photolithography components (like quartz lenses and photomasks) are poised for strong growth in this niche sector.
📢 High-Purity Quartz = The Hidden Backbone of Semiconductors
When it comes to semiconductors, all eyes are on silicon, but it’s really high-purity quartz that makes it all possible. From the initial growth of silicon ingots to the final photolithography step, every major process in semiconductor production relies on quartz. Without it, there are no chips, no smartphones, and no self-driving cars.
As demand for advanced semiconductors grows (thanks to AI, 5G, and EVs), the need for high-purity quartz will grow too. Companies that supply quartz crucibles, lenses, and etching chambers are already seeing a surge in orders. Investors looking for exposure to the semiconductor supply chain should pay close attention to companies involved in the mining, refining, and processing of high-purity quartz. This niche sector could see explosive growth as countries race to secure their semiconductor supply chains.
Whether you’re an industry insider or an investor looking for the next big opportunity, one thing is clear: High-purity quartz isn’t just part of the semiconductor story — it’s the foundation. 🚀
Table Summary
MinerGuide: 10 Reasons Why High-Purity Quartz is the Backbone of Semiconductors | ||
---|---|---|
Reason | Why It Matters | Key Insights |
Source for Silicon Wafers | High-purity quartz is refined to create ultra-pure silicon, which is the base material for all semiconductor wafers. Without it, chip production would be impossible. | Major producers like TSMC and Intel depend on ultra-high-purity silicon wafers for 2nm and 3nm chip production. Quartz with 99.999% purity (5N) is required to meet industry standards. |
Thermal Stability in Production | Quartz components like crucibles and tubes can withstand the extreme heat used in Chemical Vapor Deposition (CVD) and wafer fabrication, without deforming or contaminating the process. | Quartz’s ability to handle temperatures over 1,100°C makes it essential for semiconductor fabrication tools from suppliers like Lam Research and Applied Materials. |
Optical Clarity for Photolithography | Quartz lenses used in photolithography allow ultraviolet (UV) light to pass through with maximum clarity, enabling precise etching of microscopic patterns onto silicon wafers. | ASML’s Extreme Ultraviolet (EUV) lithography machines rely on ultra-pure quartz lenses to create 2nm and 3nm node chips used in modern AI processors and smartphones. |
Plasma Etching Support | Quartz chambers and components used in plasma etching maintain a clean, non-reactive environment to avoid contamination of wafers during the etching process. | Ionized gases in plasma etching can degrade lower-quality materials, but high-purity quartz withstands thousands of etching cycles, supporting defect-free wafer production. |
Ultra-Pure Production Environment | Quartz rods, tubes, and vessels are used in semiconductor cleanrooms to maintain ultra-clean environments, ensuring that no contaminants affect wafer production. | Cleanroom components made from quartz prevent particle shedding, and global fabs like Intel and TSMC depend on quartz rods and handling equipment for ultra-clean manufacturing. |
Contamination-Free Chemical Vapor Deposition (CVD) | Quartz reactors provide a clean environment for CVD, where thin films of silicon, oxides, or nitrides are deposited onto wafers, a critical step in chip production. | High-purity quartz prevents contamination during the CVD process, ensuring defect-free film layers on silicon wafers. Reactor tubes from Momentive and Heraeus are essential in the process. |
Ion Implantation Accuracy | During ion implantation, charged particles are fired at wafers. Quartz components keep the environment stable and contaminant-free, ensuring precise ion positioning. | Suppliers like Applied Materials rely on quartz-based wafer carriers and ion beam guides to maintain precision and reduce the risk of wafer defects during implantation. |
Quartz Crucibles for Silicon Growth | Molten silicon is grown into large crystal ingots inside high-purity quartz crucibles. The purity of the crucible directly impacts the purity of the silicon. | Companies like Samsung and GlobalFoundries depend on quartz crucibles to grow monocrystalline silicon for wafers. Heraeus and Momentive are leading suppliers of quartz crucibles. |
Supply Chain Risk Reduction | With limited sources of high-purity quartz globally, semiconductor companies are vertically integrating their supply chains to secure access to this critical raw material. | Countries like Norway, the U.S., and Brazil are key sources for high-purity quartz. Fabs like TSMC and Intel are seeking to reduce dependence on third-party suppliers for quartz crucibles and components. |
Enables Next-Gen Chips | As semiconductor nodes shrink to 2nm and 1nm, extreme precision is required in every production step. High-purity quartz plays a crucial role in every phase of production. | Photolithography, etching, and CVD processes for 2nm and 1nm chips require quartz with 5N purity. Next-gen semiconductor fabs will demand even higher-grade quartz for the future of chip production. |