7 Energy-Efficient Crushers Revolutionizing Sustainable Mining

Energy efficiency has become a top priority in mining operations as companies face increasing energy costs and stringent environmental regulations. Crushers, a cornerstone of the mining process, are now being engineered to consume less power while maintaining top-notch performance. By integrating advanced technologies and innovative designs, these energy-efficient crushers not only reduce operational costs but also align with sustainability goals. Let’s explore 7 crushers that are making a difference, starting with two groundbreaking solutions.
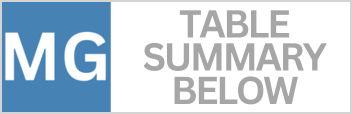
1️⃣ High-Pressure Grinding Rolls (HPGRs)
Why It’s Game-Changing:
High-Pressure Grinding Rolls (HPGRs) are renowned for their energy-saving capabilities compared to traditional crushers. They use high pressure to grind and crush ore between two rotating rolls. This compression-based crushing method drastically reduces the energy needed for further grinding, making HPGRs ideal for hard rock mining and processing.
Energy-Saving Features:
- Lower Grinding Energy: By creating micro-cracks in ore particles, HPGRs reduce the need for energy-intensive grinding in downstream processes.
- Reduced Heat Generation: The compression method minimizes energy loss due to heat, unlike impact or attrition crushers.
- Improved Wear Resistance: Modern HPGRs feature advanced wear-resistant surfaces, extending equipment lifespan and lowering maintenance costs.
Applications:
HPGRs are commonly used in copper, gold, and diamond mining operations. They are particularly effective for ores that require fine grinding, significantly improving circuit efficiency.
Example:
A major copper mine in South America integrated HPGRs into its comminution circuit, reducing energy consumption by 20% while increasing overall throughput.
2️⃣ Vertical Shaft Impact (VSI) Crushers
Why It’s Game-Changing:
VSI crushers use a unique rock-on-rock crushing principle, where materials collide with each other inside a vertical chamber. This self-crushing action not only enhances energy efficiency but also minimizes wear and tear on the crusher components, leading to lower maintenance needs.
Energy-Saving Features:
- Rock-on-Rock Design: Eliminates the need for external crushing components, drastically reducing energy usage.
- Adjustable Speed Drives: Allow operators to tailor the crushing process, ensuring optimal energy consumption for different materials.
- Minimal Dust and Noise: VSI crushers generate less environmental impact, making them a sustainable option.
Applications:
VSI crushers are widely used for producing high-quality aggregates and sand in mining and construction projects. They’re particularly useful in operations requiring uniform particle shapes and sizes.
Example:
A large gold mine in Australia replaced its traditional cone crushers with VSI units, cutting energy usage by 25% while improving product quality for downstream processing.
3️⃣ Gyratory Crushers with Variable Speed Drives
Why It’s Game-Changing:
Gyratory crushers have been a staple in mining operations for decades, but incorporating variable speed drives (VSDs) has taken their efficiency to the next level. By allowing operators to adjust the crusher’s speed to match ore characteristics and throughput demands, these crushers optimize energy usage while maintaining consistent performance.
Energy-Saving Features:
- Dynamic Speed Adjustment: Reduces energy waste by matching power output to the exact processing needs.
- Peak Energy Control: Operates efficiently even during fluctuating load conditions, minimizing energy surges.
- Longer Equipment Life: Reduces mechanical stress and wear by preventing overuse during low-demand periods.
Applications:
Gyratory crushers with VSDs are ideal for primary crushing in large-scale mining operations, including iron ore and copper mining. They excel in handling high-capacity loads with varying ore hardness.
Example:
A leading iron ore mine in Canada upgraded its gyratory crushers with VSDs, reducing power consumption by 15% and improving crusher uptime by 10%.
4️⃣ Hybrid Cone Crushers
Why It’s Game-Changing:
Hybrid cone crushers combine hydraulic and electric technologies to create a high-efficiency crushing solution. By integrating the best of both systems, they minimize energy consumption while delivering high crushing power, even for the hardest materials.
Energy-Saving Features:
- Dual-Power System: Switches seamlessly between hydraulic and electric power, ensuring maximum efficiency for varying workloads.
- Optimized Crushing Chamber: Designed to minimize friction and maximize material throughput, reducing energy losses.
- Reduced Fuel Dependence: When used in electric mode, hybrid crushers significantly cut operational fuel costs and emissions.
Applications:
Hybrid cone crushers are versatile and effective for secondary and tertiary crushing in mining operations involving gold, copper, and aggregate production.
Example:
A gold mine in South Africa implemented hybrid cone crushers, achieving a 20% reduction in fuel usage while increasing output efficiency by 18%.
5️⃣ Mobile Impact Crushers with Hybrid Engines
Why It’s Game-Changing:
Mobile impact crushers with hybrid engines offer an eco-friendly alternative to traditional diesel-powered crushers. These crushers combine electric and diesel power to deliver high performance while drastically reducing fuel consumption and emissions, making them perfect for remote mining sites.
Energy-Saving Features:
- Dual-Power System: Operates on electric power when grid access is available, switching to diesel when needed.
- Regenerative Braking: Recovers energy during operation to reduce overall fuel consumption.
- Portability: Their mobility minimizes the need for additional transport equipment, saving energy and costs.
Applications:
Ideal for smaller, remote mining operations, these crushers can handle a variety of materials, including recycled aggregates and mid-hard ores.
Example:
A limestone quarry in Europe integrated mobile impact crushers with hybrid engines, achieving a 30% reduction in fuel consumption and lowering CO2 emissions by 25%.
6️⃣ Intelligent Crusher Systems
Why It’s Game-Changing:
Intelligent crusher systems are equipped with advanced sensors and AI-driven software that monitor and optimize performance in real time. By analyzing data such as material hardness, feed rate, and power consumption, these systems ensure crushers operate at peak efficiency.
Energy-Saving Features:
- Real-Time Adjustments: AI fine-tunes settings to minimize energy waste while maximizing output.
- Predictive Maintenance: Reduces downtime by identifying potential issues before they occur, improving energy efficiency.
- Adaptive Workflows: Adjusts operation based on changing conditions, such as feed size or ore type.
Applications:
Intelligent crushers are suitable for large-scale mining operations handling diverse materials, from hard rock to softer ores.
Example:
A copper mine in South America deployed intelligent crushers, resulting in a 20% increase in energy efficiency and a 15% reduction in operational downtime.
7️⃣ Eco-Friendly Jaw Crushers
Why It’s Game-Changing:
Modern jaw crushers have been redesigned with eco-friendly features that drastically improve energy efficiency without compromising crushing power. They are built with optimized crushing angles, low-friction components, and advanced automation to reduce both energy consumption and environmental impact.
Energy-Saving Features:
- Improved Crushing Mechanics: Redesigned angles and components minimize energy loss during operation.
- Efficient Motors: Use energy-efficient electric motors that meet the latest environmental standards.
- Noise and Dust Reduction: Incorporate advanced sealing and dampening systems to reduce noise pollution and minimize dust emissions.
Applications:
Perfect for primary crushing in mining operations, eco-friendly jaw crushers are used for processing materials like iron ore, granite, and limestone.
Example:
A granite quarry in India replaced its older jaw crushers with eco-friendly models, cutting power usage by 22% and meeting local environmental compliance standards.
Energy-efficient crushers are transforming the mining industry by helping operators reduce energy consumption, lower costs, and meet sustainability goals. From high-pressure grinding rolls to intelligent crusher systems, these innovations prove that it’s possible to combine performance with environmental responsibility.
As energy prices rise and environmental regulations tighten, investing in energy-efficient crushers isn’t just a smart financial decision—it’s a commitment to a more sustainable future in mining. By embracing these technologies, mining operations can stay ahead of the curve and contribute to a greener planet while maintaining high productivity. 🌍💎
Table Summary
MinerGuide: Energy-Efficient Crushers for Sustainable Mining Operations | |||
Crusher Type | Key Features | Advantages | Example Use Case |
High-Pressure Grinding Rolls (HPGRs) |
– Compression-based crushing method – Creates micro-cracks in ore – Reduces grinding energy needs |
– Cuts energy consumption in grinding processes – Minimizes heat loss during operation – Durable wear-resistant surfaces lower maintenance costs |
Used in a copper mine in South America to reduce energy usage by 20% while increasing throughput. |
Vertical Shaft Impact (VSI) Crushers |
– Rock-on-rock crushing principle – Adjustable speed drives – Minimal dust and noise generation |
– Reduces energy waste – Enhances aggregate quality – Low maintenance requirements due to reduced wear |
Deployed in a gold mine in Australia, cutting energy use by 25% and improving product quality. |
Gyratory Crushers with Variable Speed Drives |
– Dynamic speed adjustment – Handles high-capacity loads – Operates efficiently under fluctuating demand |
– Optimizes energy use during low-demand periods – Extends equipment lifespan – Reduces operational costs |
Used in a Canadian iron ore mine, reducing power consumption by 15% and increasing uptime by 10%. |
Hybrid Cone Crushers |
– Combines hydraulic and electric technologies – Dual-power system – Optimized crushing chambers |
– Reduces fuel dependency – Delivers high throughput – Minimizes friction, enhancing efficiency |
Implemented in a South African gold mine, reducing fuel use by 20% and boosting efficiency by 18%. |
Mobile Impact Crushers with Hybrid Engines |
– Hybrid diesel-electric system – Regenerative braking – Portable and flexible |
– Reduces fuel consumption – Cuts CO2 emissions – Ideal for remote sites |
Deployed in a European limestone quarry, reducing fuel usage by 30% and emissions by 25%. |
Intelligent Crusher Systems |
– AI-driven real-time monitoring – Adaptive workflows – Predictive maintenance |
– Optimizes energy consumption – Minimizes downtime – Adapts to changing conditions |
Used in a South American copper mine, increasing energy efficiency by 20% and reducing downtime by 15%. |
Eco-Friendly Jaw Crushers |
– Low-friction components – Optimized crushing angles – Noise and dust reduction |
– Cuts power usage – Meets environmental standards – Reduces noise and dust pollution |
Replaced older models in an Indian granite quarry, lowering energy usage by 22% and meeting compliance standards. |